About Maxsure
Maxsure Engineering Private Limited (MEPL) is a premier independent inspection, testing, and certification company, providing a broad spectrum of services across various industries with a focus on agricultural, food, mechanical, and electrical products. With over a decade of experience, MEPL has built a strong reputation for delivering accurate, reliable, and impartial inspections that help our clients meet regulatory standards, improve product quality, and mitigate risks in global markets.
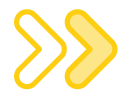
At MEPL, we are dedicated to ensuring that our clients’ products meet the highest standards of safety, quality, and compliance. We combine technical expertise, state-of-the-art testing facilities, and a global presence to offer a wide range of inspection and certification services that cater to the needs of manufacturers, exporters, importers, and suppliers.
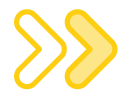
MEPL has wide network of engineers covering every corner of India.
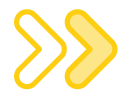
MEPL has multinational engineering and third party inspections (TPI) companies as clients
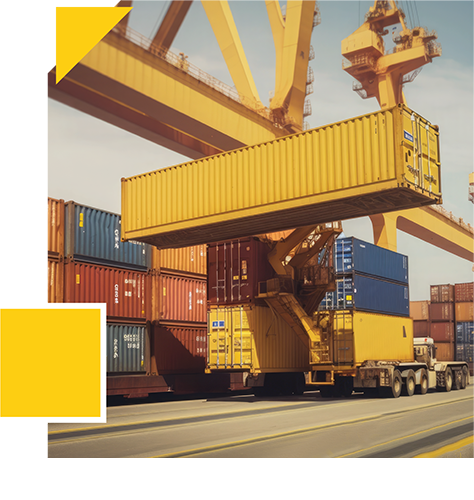
Who We Are
MEPL is committed to delivering high-quality inspection, testing, and certification services. With a focus on reliability and innovation, we have established ourselves as a leader in agricultural, food, mechanical, and electrical product sectors. Our skilled team and customer-first approach have made MEPL a trusted partner for businesses worldwide.
Accreditation
Who We Are
Accreditation
Why Choose MEPL ?
- Unmatched Expertise: Our team’s deep knowledge across industries, combined with state-of-the-art technologies, ensures high-quality, precise inspection services.
- Global Reach, Local Expertise: With a global presence and local expertise, we provide services across borders while ensuring compliance with both regional and international standards.
- Accredited & Trusted: MEPL operates with full accreditation and certification, adhering to the highest standards of integrity and transparency in all our inspection services.
- Tailored Solutions: We offer customized inspection and certification services, ensuring that we meet the unique requirements of each client and project.
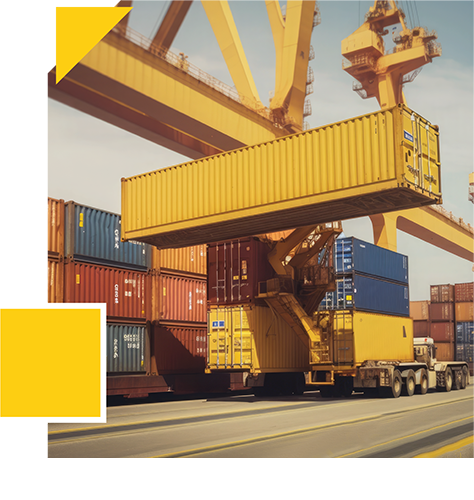
What We Do
Shop & Site Inspection
Inspection at manufacturing
location before shipment
Independent and detailed
assessment reassures the quality
and quantity confirmations
Witness Tests
We perform witness tests
according to the International
Standards and the client
requirements QA & QC Audit
QA & QC audit to certify the
processes and benchmarking
against best practice
Factory audits
Inspection & Expediting
Facilitate presence of expediting
managers to assure timely delivery and cost management
Our Approach
- Dedicated team of qualified engineers and project managers for large projects
- Regional & Functional coordinators for quick turn around
- Surveyors with fitting qualification and experience is deployed for each assignment
- Inspection scheduling is completed within 2 days for local and 3 days for outstation location
- We value time: our surveyors arrive at appointed time and cooperate during extra hours
- Real time interaction with client from onsite to resolve issues
- Detailed reports with accurate findings, reliable information and enhanced analysis
- Reports, supporting documents and site photographs, validating our findings, are reported within twenty four hours of the completion of the inspection
- Digital back up for reports, records, photographs and related documents for twelve months
Our Team
Global Network and Local Expertise
At MEPL, we pride ourselves on the quality of our workforce. Our team is composed of highly skilled professionals who bring expertise from various industries, including agriculture, food safety, engineering, and quality assurance. Each team member undergoes continuous training to stay abreast of the latest industry standards and regulatory changes.
Agronomists & Food Safety Experts
Specializing in agricultural product quality, food safety, and compliance, our team helps ensure that agricultural and food products meet both national and international standards.
Mechanical & Electrical Engineers
Our engineers are equipped with the technical knowledge to inspect and test complex mechanical and electrical systems, ensuring compliance with industry-specific standards such as CE, UL, and IEC.
Quality Control Specialists:
They ensure that every inspection and testing procedure adheres to stringent quality guidelines, maintaining the integrity of our certification processes.
Our Policy
Maxsure Engineering Pvt. Ltd. is dedicated to the principles of impartiality across all facets of our inspection activities. This policy serves as a comprehensive outline of our commitment to ensuring unbiased and fair practices, aligning with international standards and regulations.
Scope:
This policy is applicable to all personnel engaged in inspection activities, including employees, contractors, and third-party associates affiliated with Maxsure Engineering Pvt. Ltd.
Commitment to Impartiality:
At Maxsure Engineering Pvt. Ltd., we affirm our commitment to maintaining objectivity in all inspection activities, steadfastly avoiding conflicts of interest that could compromise impartiality. Our pledge includes conducting inspections without favouritism or bias towards any client, thereby ensuring equal treatment for all entities undergoing assessment.
Independence and Integrity:
Our personnel involved in inspection activities adhere to a commitment to independent decision-making, free from any undue influence. We emphasize transparency in our decision-making processes, providing clear rationales and documentation for conclusions reached during inspections.
Identification and Management of Conflicts:
To fortify impartiality, we establish a robust conflict of interest policy. This policy enables the identification, assessment, and effective management of potential conflicts that may compromise impartiality. Our personnel are obligated to promptly disclose any personal or financial interests that could be perceived as conflicting with the impartiality of inspection activities.
Continuous Monitoring and Improvement:
To ensure ongoing adherence to impartiality principles, Maxsure Engineering Pvt. Ltd. conducts regular internal audits. These audits assess the effectiveness of measures in place to maintain impartiality. We also implement feedback mechanisms to encourage the reporting of any perceived lapses in impartiality, fostering a culture of continuous improvement.
Training and Awareness:
A cornerstone of our impartiality commitment is comprehensive training for all personnel. Through this training, we raise awareness about the significance of impartiality in inspection activities. Additionally, scenario-based training exercises are conducted to enhance personnel’s ability to recognize and address situations that may compromise impartiality.
Communication and Documentation:
We establish clear communication channels to ensure relevant stakeholders are informed of the steps taken to maintain impartiality. Our impartiality-related procedures are meticulously documented, promoting transparency and providing a comprehensive reference for all personnel.
Top management and inspection personnel identifies and assess risks in all relationships that may result in a conflict of interest and pose a threat to impartiality. Threats to impartiality include, but are not limited to, the following:
Moreover, our inspection has documented structures, policies and procedures to manage impartiality and to ensure that the relevant activities are undertaken impartially.
This Inspection body’s top management recognizes that impartiality is important to our clients and other stakeholders and commits to ensuring impartiality in all Inspection activities.
- Cause new conflicts of interest can surface over time, top management and inspection personnel participate in a risk assessment annually to ensure ongoing impartiality and identify new potential conflicts of interest relating to the inspection activities performed by our laboratory.
- Conflict of interest and objectivity are further addressed in our Code of Conduct and through contractually binding agreements that ensure inspection activities are conducted in an independent and impartial manner.
Financial threats: the source of revenue for an inspection or it’s personnel can a threat to impartiality.
Intimidation threats: threats that prevent an inspection or its personnel from acting objectively due to fear of a client or other interested stakeholder.
Familiarity threats: threats that arise from a person familiar with or trusting of another person, e.g., top management or inspection personnel developing a relationship with a client that affects the ability to reach an objective judgment.
- Subjectivity threats: threats that arise when personal bias overrules objective evidence.
- Self-interest threats: threats that arise from a person or body acting in its own interest to benefit itself.
- The Management of Maxsure Engineering Pvt. Ltd. understands and acknowledges the importance of impartiality and that there are potential conflicts of interest that can arise when performing inspection activities.
Confidentiality of Information:
In alignment with our impartiality commitment, confidential information related to clients and inspection activities is handled with the utmost care. This ensures the preservation of impartiality and prevents any compromise due to improper handling of sensitive information.
In carrying out its activities, Maxsure Engineering Pvt. Ltd. called upon to obtain confidential information concerning individuals and/or organizations. Maxsure Engineering Pvt. Ltd. places great importance on respecting the privacy of the individuals who use its inspection services. It has therefore introduced a series of rigorous policies and procedures designed to protect user privacy. The information below provides an overview of Maxsure Engineering Pvt. Ltd. commitment regarding privacy and confidentiality.
Data Inputting and Transmission
The information that our inspection body receives when an order and/or request for information is placed is treated with the utmost confidentiality. Our inspection body does not disclose the names of, or information on, individuals and/or organizations that are in contact with it. The Inspection data conducted by our inspection body are transmitted by registered email to the authorized persons. The inspection engineers do not give any information over the telephone or fax.
Before discussing specific cases over the telephone, our inspection body staff ask many questions to validate the caller’s identity.
Employees
The handling of confidential information within our inspection body is strictly limited to those employees who require access to carry out their functions. Thus, during the hiring process, the inspection body performs checks on candidates’ employment history and background. These checks may include credit checks, criminal record checks, inquiries into their professional training and checks with former employers. Once hired, employees must sign a confidentiality agreement with our inspection body, which agreement includes specific provisions regarding the confidentiality of information obtained during work. During their employment at our inspection body, employees are regularly reminded of the importance of respecting the confidentiality of information obtained during their duties.
Subcontractors
Our subcontractors who assist us with overflow work, are extensively screened and are required to complete a Subcontractor Agreement prior to engaging in any work. The Subcontractor Agreement includes relevant nondisclosure and non-solicitation clauses.
Only the pertinent materials and critical information necessary for completion of the task by our subcontractors, is given to our subcontractors, and only on a need-to-know basis.
This Impartiality Policy is an integral component of our commitment to quality, compliance, and ethical conduct in all inspection activities at Maxsure Engineering Pvt. Ltd.
Maxsure Engineering Pvt. Ltd .is committed to good professional practice through Inspection Services.
Our mission is to supply on-time delivery of inspection results and services, which are of the best possible quality and consistently meet the performance criteria.
In order to live up to our Quality Policy and Objectives, Maxsure Engineering Pvt. Ltd. execute inspections in efficient manner, and on time as per Inspection methods that consistently meet or exceed our client’s requirements. This is accomplished through a continuing program to improve upon operational procedures and systems while striving to supply accurate and exact inspection results. Maxsure Engineering Pvt. Ltd. believes in “Creating Value, Delivering Excellence” to our esteemed clients.
Inspections services provided by Maxsure Engineering Pvt. Ltd. conform to the requirements specified by client and be performed under the ISO 17020 :2012 Standard. Management’s responsibility is to provide direct leadership and resources to ensure continued conformance with these requirements. A corner stone of Maxsure Engineering Pvt. Ltd.’ Policy is that excellence in the quality of the inspections service is the result of collective effort and commitment from all its team members.
The quality system is under regular review and audit. All employees are invited to suggest possible improvements in working practice to the management. Quality Policy provides a framework for establishing and reviewing context, quality objectives and continuing its suitability.
Financial or political considerations do not influence the quality of the Inspection activities of Maxsure Engineering Pvt. Ltd.
Maxsure Engineering Pvt. Ltd.’ key Quality objectives for the Inspection services are:
- Ensure that our Inspection methods are reliable, verifiable and confirm to National/International/Client-specific standards;
- Ensuring Integrity of our people, processes, Business related information and systems;
- Zero Conflicts of Interest;
- Ensuring Confidentiality and data protection;
- Complying with Anti Bribery stipulations;
- Maintaining Fair Business Conduct at all times;
- Ensuring Health & Safety of our team and within our work environment;
- Follow Fair Labor practices in sync with local laws;
- Ensure a systematic and process-oriented approach;
- Maintain a management system in accordance with the accreditation standards ISO/IEC 17020:2012
Maxsure Engineering Pvt. Ltd. is dedicated to the principles of impartiality across all facets of our inspection activities. This policy serves as a comprehensive outline of our commitment to ensuring unbiased and fair practices, aligning with international standards and regulations.
Scope:
This policy is applicable to all personnel engaged in inspection activities, including employees, contractors, and third-party associates affiliated with Maxsure Engineering Pvt. Ltd.
Commitment to Impartiality:
At Maxsure Engineering Pvt. Ltd., we affirm our commitment to maintaining objectivity in all inspection activities, steadfastly avoiding conflicts of interest that could compromise impartiality. Our pledge includes conducting inspections without favouritism or bias towards any client, thereby ensuring equal treatment for all entities undergoing assessment.
Independence and Integrity:
Our personnel involved in inspection activities adhere to a commitment to independent decision-making, free from any undue influence. We emphasize transparency in our decision-making processes, providing clear rationales and documentation for conclusions reached during inspections.
Identification and Management of Conflicts:
To fortify impartiality, we establish a robust conflict of interest policy. This policy enables the identification, assessment, and effective management of potential conflicts that may compromise impartiality. Our personnel are obligated to promptly disclose any personal or financial interests that could be perceived as conflicting with the impartiality of inspection activities.
Continuous Monitoring and Improvement:
To ensure ongoing adherence to impartiality principles, Maxsure Engineering Pvt. Ltd. conducts regular internal audits. These audits assess the effectiveness of measures in place to maintain impartiality. We also implement feedback mechanisms to encourage the reporting of any perceived lapses in impartiality, fostering a culture of continuous improvement.
Training and Awareness:
A cornerstone of our impartiality commitment is comprehensive training for all personnel. Through this training, we raise awareness about the significance of impartiality in inspection activities. Additionally, scenario-based training exercises are conducted to enhance personnel’s ability to recognize and address situations that may compromise impartiality.
Communication and Documentation:
We establish clear communication channels to ensure relevant stakeholders are informed of the steps taken to maintain impartiality. Our impartiality-related procedures are meticulously documented, promoting transparency and providing a comprehensive reference for all personnel.
- The Management of Maxsure Engineering Pvt. Ltd. understands and acknowledges the importance of impartiality and that there are potential conflicts of interest that can arise when performing inspection activities.
- Cause new conflicts of interest can surface over time, top management and inspection personnel participate in a risk assessment annually to ensure ongoing impartiality and identify new potential conflicts of interest relating to the inspection activities performed by our laboratory.
Top management and inspection personnel identifies and assess risks in all relationships that may result in a conflict of interest and pose a threat to impartiality. Threats to impartiality include, but are not limited to, the following:
- Self-interest threats: threats that arise from a person or body acting in its own interest to benefit itself.
- Subjectivity threats: threats that arise when personal bias overrules objective evidence.
- Familiarity threats: threats that arise from a person familiar with or trusting of another person, e.g., top management or inspection personnel developing a relationship with a client that affects the ability to reach an objective judgment.
- Intimidation threats: threats that prevent an inspection or its personnel from acting objectively due to fear of a client or other interested stakeholder.
- Financial threats: the source of revenue for an inspection or it’s personnel can a threat to impartiality.
- Conflict of interest and objectivity are further addressed in our Code of Conduct and through contractually binding agreements that ensure inspection activities are conducted in an independent and impartial manner.
Moreover, our inspection has documented structures, policies and procedures to manage impartiality and to ensure that the relevant activities are undertaken impartially.
This Inspection body’s top management recognizes that impartiality is important to our clients and other stakeholders and commits to ensuring impartiality in all Inspection activities.
Confidentiality of Information:
In alignment with our impartiality commitment, confidential information related to clients and inspection activities is handled with the utmost care. This ensures the preservation of impartiality and prevents any compromise due to improper handling of sensitive information.
In carrying out its activities, Maxsure Engineering Pvt. Ltd. called upon to obtain confidential information concerning individuals and/or organizations. Maxsure Engineering Pvt. Ltd. places great importance on respecting the privacy of the individuals who use its inspection services. It has therefore introduced a series of rigorous policies and procedures designed to protect user privacy. The information below provides an overview of Maxsure Engineering Pvt. Ltd. commitment regarding privacy and confidentiality.
Data Inputting and Transmission
The information that our inspection body receives when an order and/or request for information is placed is treated with the utmost confidentiality. Our inspection body does not disclose the names of, or information on, individuals and/or organizations that are in contact with it. The Inspection data conducted by our inspection body are transmitted by registered email to the authorized persons. The inspection engineers do not give any information over the telephone or fax.
Before discussing specific cases over the telephone, our inspection body staff ask many questions to validate the caller’s identity.
Employees
The handling of confidential information within our inspection body is strictly limited to those employees who require access to carry out their functions. Thus, during the hiring process, the inspection body performs checks on candidates’ employment history and background. These checks may include credit checks, criminal record checks, inquiries into their professional training and checks with former employers. Once hired, employees must sign a confidentiality agreement with our inspection body, which agreement includes specific provisions regarding the confidentiality of information obtained during work. During their employment at our inspection body, employees are regularly reminded of the importance of respecting the confidentiality of information obtained during their duties.
Subcontractors
Our subcontractors who assist us with overflow work, are extensively screened and are required to complete a Subcontractor Agreement prior to engaging in any work. The Subcontractor Agreement includes relevant nondisclosure and non-solicitation clauses.
Only the pertinent materials and critical information necessary for completion of the task by our subcontractors, is given to our subcontractors, and only on a need-to-know basis.
This Impartiality Policy is an integral component of our commitment to quality, compliance, and ethical conduct in all inspection activities at Maxsure Engineering Pvt. Ltd.
Maxsure Engineering Pvt. Ltd .is committed to good professional practice through Inspection Services.
Our mission is to supply on-time delivery of inspection results and services, which are of the best possible quality and consistently meet the performance criteria.
In order to live up to our Quality Policy and Objectives, Maxsure Engineering Pvt. Ltd. execute inspections in efficient manner, and on time as per Inspection methods that consistently meet or exceed our client’s requirements. This is accomplished through a continuing program to improve upon operational procedures and systems while striving to supply accurate and exact inspection results. Maxsure Engineering Pvt. Ltd. believes in “Creating Value, Delivering Excellence” to our esteemed clients.
Inspections services provided by Maxsure Engineering Pvt. Ltd. conform to the requirements specified by client and be performed under the ISO 17020 :2012 Standard. Management’s responsibility is to provide direct leadership and resources to ensure continued conformance with these requirements. A corner stone of Maxsure Engineering Pvt. Ltd.’ Policy is that excellence in the quality of the inspections service is the result of collective effort and commitment from all its team members.
The quality system is under regular review and audit. All employees are invited to suggest possible improvements in working practice to the management. Quality Policy provides a framework for establishing and reviewing context, quality objectives and continuing its suitability.
Financial or political considerations do not influence the quality of the Inspection activities of Maxsure Engineering Pvt. Ltd.
Maxsure Engineering Pvt. Ltd.’ key Quality objectives for the Inspection services are:
- Ensure that our Inspection methods are reliable, verifiable and confirm to National/International/Client-specific standards;
- Ensuring Integrity of our people, processes, Business related information and systems;
- Zero Conflicts of Interest;
- Ensuring Confidentiality and data protection;
- Complying with Anti Bribery stipulations;
- Maintaining Fair Business Conduct at all times;
- Ensuring Health & Safety of our team and within our work environment;
- Follow Fair Labor practices in sync with local laws;
- Ensure a systematic and process-oriented approach;
- Maintain a management system in accordance with the accreditation standards ISO/IEC 17020:2012